Common Challenges In Implementing Safety Instrumented Systems (SIS) And How To Overcome Them
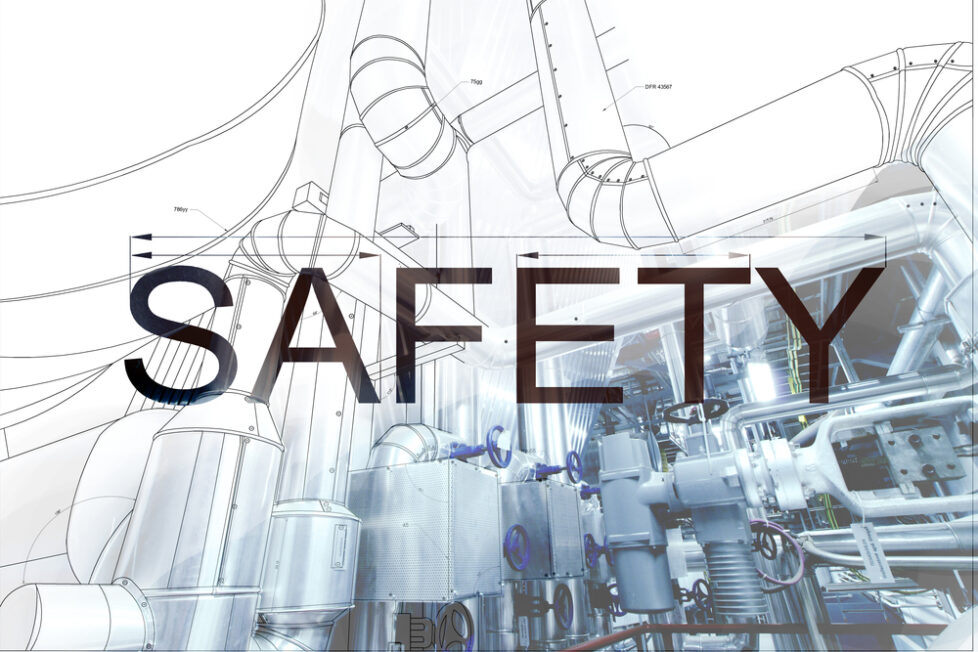
Safety instrumented systems (SIS) play a critical role in monitoring hazardous industrial processes and taking action to prevent such disasters from taking place. However, implementing and managing SIS comes with a unique set of challenges that company owners, plant managers, safety officers, and the like must be prepared for.
Luckily, this guide aims to lend a helping hand. The points below will define what safety instrumented systems are. They will go over the most common implementation challenges surrounding carrying out SIS, provide workable solutions to overcome them, and so on. In addition, it’ll include examples and key takeaways for SIS implementation and deployment success.
Read on to learn more.
To begin, it’s best to tackle the elephant in the room: what does SIS entail?
SIS comprises sensors, logic solvers, final control elements, and an actuation subsystem that work in unison to take a process to a safe state when predetermined unsafe or abnormal conditions are detected. SIS forms one essential layer of protection in a process plant’s or a given establishment’s overall safety strategy and works alongside basic process control systems that are in place.
While the architecture varies, well-designed SIS have four key components you should know about:
All four elements must work together flawlessly to achieve process safety. Redundancy is built in to avoid single points of failure.
Nothing’s perfect in this world – and that statement holds, especially concerning SIS.
While SIS offers crucial protection, several common factors can undermine SIS performance if not properly addressed by plant managers, safety officers, company owners, and the like. They include the following:
One widespread issue is a lack of adequate training on SIS principles for operators and technicians. They may not sufficiently understand how to interpret SIS alarms and warnings, what actions to take, or when the system requires maintenance. This knowledge gap surrounding SIS operation can lead to improper responses or interventions during emergencies.
Luckily, providers like orion-technical.com can help with such SIS implementation predicaments.
Integrating the SIS system with the basic process control system is incredibly complex and requires deep expertise. If the integration isn’t seamless, operators can experience nuisance trips of the SIS that undermine trust in the system’s value. Similarly, without tight integration, operators may miss critical alarms.
SIS requires structured management of change (MOC) procedures to handle modifications to the system. Nonetheless, many sites are said to lack robust MOC policies for SIS. Introducing changes without thoroughly evaluating the impact on overall safety can allow risks to slip through the cracks.
SIS has significant lifecycle costs that must be planned for, including routine maintenance, testing, calibration, upgrades, and eventual replacement. Insufficient planning and budgeting for these long-term costs can lead to declining SIS performance over time.
Various industry and safety standards apply to SIS design and performance. A lack of compliance means an increased risk of incidents and substantial legal exposure. Keeping current as standards evolve is critical but challenging.
With the increasing connectivity of SIS, cybersecurity threats are a growing challenge. Lacking proper network segregation, access controls, and monitoring makes systems susceptible to attack.
Besides integrating with the BPC system, SIS must also connect with emergency shutdown systems, fire and gas monitoring, and other platforms. Lacking integration hampers overall site safety.
After combing through some of the most common pain points of SIS implementation, what strategies can plant managers, engineers, and other stakeholders employ to overcome them? Continue reading to find out.
Make ongoing training on SIS operation a top priority. This includes classroom learning on fundamentals as well as frequent simulator exercises. Employees should thoroughly understand SIS architecture, purpose, functionality, and proper response to alarms. Training improves competence and compliance.
Pay close attention to integration details when connecting SIS with other plant systems. Follow standards, clearly delineate functions, and encourage frequent communication between integration teams. Well-executed integration prevents dangerous gaps.
Have structured MOC policies requiring cross-disciplinary review and sign-off before any modifications are made to the SIS. Every change should be evaluated for its impact on overall plant safety. This prevents unintended consequences.
Develop comprehensive lifecycle management plans that account for upfront, mid-life, and end-of-life SIS expenditures. Closely monitor system health and perform proactive maintenance. This reduces the risk of declining effectiveness.
Assign clear responsibility for compliance with SIS standards. Conduct internal audits, stay current on evolving regulatory changes, and maintain necessary documentation. Keeping compliant is a legal obligation.
Implement modern best practices for SIS cybersecurity, including network segmentation, access management, monitoring, and patching. Cyber risks can undermine safety if not addressed.
Encourage team member engagement by forging a work culture that allows individuals to be able to provide work-related feedback. To proceed, set in place reporting and feedback mechanisms and media to allow team members to share their insights concerning site safety, systems efficacy, and the like.
To see how the abovementioned solutions apply in practice, consider these examples:
Company X struggled with frequent SIS trips due to operator confusion. After investing in classroom and simulator training, nuisance trips were reduced by 70%.
On the other hand, Company Y had SIS integrated ad hoc, leading to a dangerous failure. By re-doing integration per ISA standards, they eliminated the issue.
Finally, Company Z failed to account for ageing transmitters in lifecycle planning. Replacing them all at once led to a USD$2 million unbudgeted expenditure.
Safety instrumented systems provide essential protection for hazardous processes, but only with proper implementation and management.
Investing in training, seamless integration, robust MOC procedures, lifecycle budgets, regulatory compliance, and cybersecurity helps companies avoid common pitfalls. With diligence across functions, organizational leaders, plant managers, safety officers, and so on can harness huge benefits from SIS while avoiding safety-related incidents.
Samantha is an HR practitioner who has worked with several companies to help them improve their HR practices. Samantha has gained decades of experience in handling all HR facets that include managerial relations, labour relations, training and development, recruitment, and compensation and benefits.
When Samantha is not busy at work, she writes articles about the importance of effective HR practices and why startups should always prioritize this area of the business.