How Much Should You Be Relying On Automated Processes In The Logistics Industry
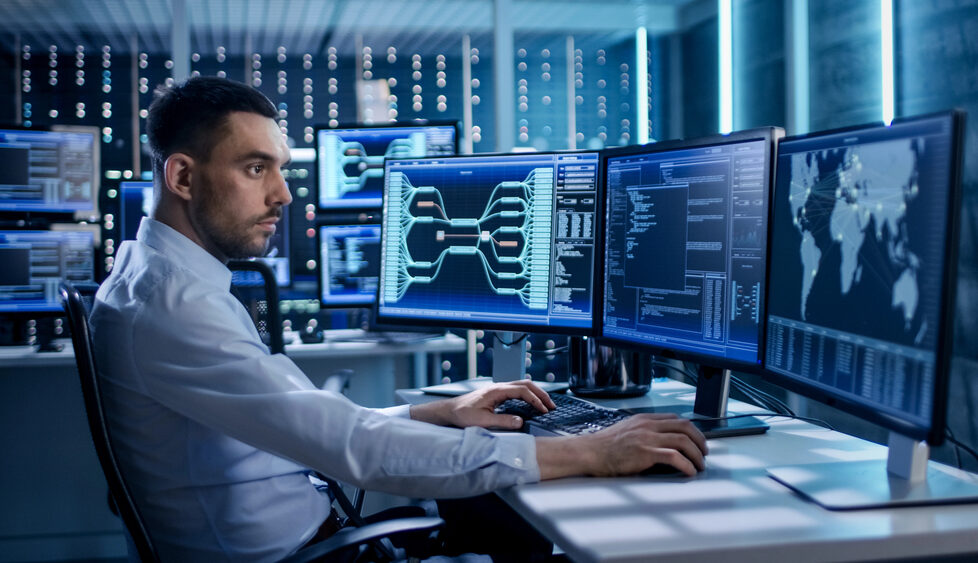
In pretty much all industries, the past century or so has been defined by a push towards increasingly complex forms of technologically driven automation. From car manufacturing to agriculture, we now have access to more ways of increasing efficiency and reducing the need for human labour than ever before, but does it come at a cost? Here, we explore some of the risks (and benefits) associated with relying on automated processes in the logistics industry. Read on for a nuanced discussion that may change the way you think about this complex topic.
To start, it’s worth mentioning that automation is unavoidable nowadays. Whether we’re talking about route planning or optimising warehouse storage, it’s no longer a competitive solution to do these things using human ingenuity alone.
The positive effects that automation has in pretty much every area of the logistics industry, from planning to execution, mean that it’s simply not competitive to avoid using these tools.
There are numerous benefits associated with adopting automated solutions in the logistics industry. Whether we’re talking about automated loading solutions from providers like Joloda Hydraroll or demand prediction algorithms driven by the latest AI, the advantages are too big to ignore.
With automated loading solutions, for example, you can massively slash the time it takes to load and unload lorries while substantially reducing the number of personnel needed for that process.
Of course, just because you’re using some automated process doesn’t mean you can just eliminate human operators. Whether we’re talking about route planning or loading processes, automation is never entirely infallible – humans are still required to check the results and lend a steering hand when necessary.
Despite the leaps and bounds that have been made in various areas of technological innovation in recent decades, this doesn’t appear to be changing any time soon. Employees need to be trained and upskilled on how to work alongside machines, to help keep them in check.
If there are specific areas of automation in your logistics operations that are both particularly vulnerable and essential for business continuity, then you should think about ways of limiting overreliance on a specific solution.
That could mean having some alternative backup in place, or a hyper-reliable way of getting that solution up and running again in case it does start to fail. There’s no single way of approaching this, and you’ll have to get creative – make sure that you consider all possible (and probable) vulnerabilities, and come up with solutions before they’re necessary.
A high level of reliance on automated solutions is unavoidable in the logistics industry. What you can do, however, is limit how vulnerable you are if these solutions go wrong. By maintaining a certain level of human oversight and limiting overreliance on specific systems, you can help maintain business continuity if disaster strikes.