Choosing the Right Tools for a Turning Shop
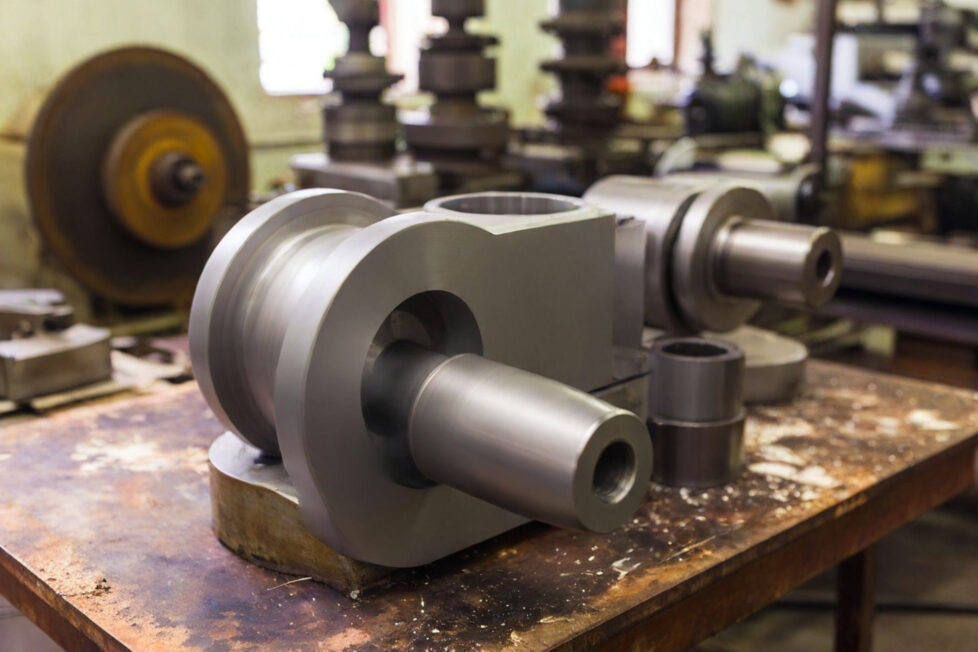
The success of a turning shop relies heavily on selecting the right tools and equipment to optimize precision, efficiency, and cost. A well-equipped shop must integrate cutting tools tailored for specific machining tasks, robust work-holding devices to secure parts, and precision measuring tools to ensure dimensional accuracy. Equally important are lubrication and coolant systems, which minimize heat buildup and extend tool life.
By understanding the specific requirements of each machining operation and aligning them with the appropriate tools, turning shops can significantly enhance their ability to provide custom CNC turning services and meet the demands of modern manufacturing challenges.
Choosing the right turning tools involves careful evaluation of material compatibility, tool geometry, and machining conditions.
The hardness, tensile strength, and machinability of the workpiece material directly influence tool selection. For example, cutting harder materials like stainless steel or titanium requires carbide or ceramic tools, while softer materials like aluminium may only need high-speed steel (HSS) tools.
Besides, for materials prone to generating excessive heat during machining, tools with high thermal resistance are crucial to maintain cutting integrity. For instance, a Titanium nitride (TiN) layer or diamond coating improves service life and heat resistance.
The rake angle, clearance angle, and cutting-edge design should be matched to the material and desired finish. Positive rake angles are better for soft materials, while negative rakes are suitable for tougher materials. Also, the shape (e.g., round, square, triangular) affects the cutting stability and finish, while the insert size determines the tool’s ability to handle heavy cuts or fine detail work.
Enhanced Performance: Coatings like titanium nitride (TiN), titanium aluminium nitride (TiAlN), or diamond-like coatings reduce friction, improve heat resistance, and extend tool life.
Material-Specific Coatings: For instance, TiN coatings work well with steel, while diamond-like coatings are ideal for machining non-ferrous materials like aluminium or composites.
To explore innovative 3D modelling techniques, chatbot integrations, and software solutions that enhance machining and manufacturing workflows, visit Botbrainers. Our platform provides cutting-edge tools and insights tailored to meet the evolving needs of industries worldwide.
Customization is key to optimizing performance in a turning shop. Custom rapid manufacturing services enable turning shops to design and implement bespoke solutions, such as specialized tool geometries and unique coatings, to suit challenging materials or complex part designs. This level of customization ensures optimal cutting performance, reduced tool wear, and higher precision in demanding applications.
Custom tools can be designed to match the geometry and dimensions of unique workpieces, ensuring better fit and efficiency. For instance, specialized inserts or cutters can be developed for intricate operations, reducing the need for multiple tool changes.
Tools customized for specific workpiece materials, such as composites or high-strength alloys, provide enhanced durability and precision. This minimizes wear and tear, particularly in demanding environments like aerospace or medical manufacturing.
Customized tools enable fine-tuning of cutting speeds, feed rates, and depths of cut, resulting in higher machining efficiency and better surface finishes. Adjusting these parameters can also reduce thermal stress on tools, prolonging their service life.
Direct business relations with the rapid manufacturing providers through strategic partnerships guarantee that only customized solutions for every project are procured. Even though it may be expensive in the short run to buy customized tools for use, they are cheaper in the long run because they work effectively, and in one transition, they are able to produce massive outputs of standardized quality with minimal disruption.
Tool holders are fundamental to the stability and precision of turning operations. They securely fasten cutting tools to the machine, ensuring consistent performance during high-speed machining. By reducing tool deflection and vibration, tool holders enhance cutting accuracy and prolong tool life. High-quality tool holders, such as modular or quick-change designs, streamline tool replacement processes, minimizing machine downtime and improving operational efficiency.
Chucks and collets play a critical role in firmly gripping the workpiece during turning. They provide the necessary stability to prevent movement or misalignment, especially in high-torque operations. Precision-engineered chucks and collets ensure uniform gripping force, which reduces the risk of distortion on delicate or complex workpieces. Their compatibility with automated systems also supports faster setups and higher production rates in turning shops.
Precision measuring instruments are indispensable for maintaining quality and ensuring that machined parts meet design specifications. Tools such as micrometers, dial indicators, and bore gauges allow operators to verify dimensions, tolerances, and surface finishes during and after machining. These instruments enhance quality control by enabling real-time adjustments and reducing scrap rates, ensuring the final product meets industry standards.
By employing these accessories effectively, turning shops can achieve significant improvements in precision, productivity, and overall operational efficiency.
Technological advancements are reshaping the landscape of turning tools, offering unparalleled efficiency and precision.
Adaptive Control System with sensor-integrated tool condition monitoring makes it possible to monitor tool condition, cutting force and temperature in real-time to predict tool wearing and, in turn, avoid periodic downtimes.
The integration of AI-driven algorithms allows for the optimization of machining parameters, reducing waste and enhancing overall productivity in manufacturing processes.
Multi-layer and Nano coatings are added to enhance wear properties and help to increase the life of the cutting tool.
Most applications involve cutting; cutting tools include turning, milling, and drilling that can be easily provided by a given tool without having to change very often, hence flexibility.
The evolution of tool materials, such as ceramic composites and cermet blends, contributes to higher cutting speeds and prolonged durability.
Thus, independent of the details regarding the implementation of these tools and systems, turning shops can sustain a competitive edge in a saturated market.
Choosing the right tools for a turning shop is a cornerstone of achieving precision, efficiency, and cost-effectiveness in machining operations. From selecting tools tailored to the workpiece material to ensuring proper tool geometry, coatings, and compatibility with cutting parameters, each decision plays a pivotal role in enhancing performance.
Incorporating advanced accessories further elevates the capabilities of custom CNC turning service and rapid manufacturing, enabling it to meet the diverse and evolving demands of modern manufacturing. By aligning tools and technologies with specific machining needs, turning shops can maximize productivity, reduce downtime, and deliver high-quality outcomes consistently.